The average cost to build a commercial warehouse is $3,100 per square foot. The cost of construction materials is only one factor in determining the overall cost of building a warehouse. Other factors that must be considered are labor, contractor services and architect fees.
Labor Costs
Labor costs for commercial construction projects vary depending on the region of the country and the specific construction project being completed. Plumbers, electricians and other skilled craftsmen can charge anywhere from $45 to $65 an hour for their services. Unskilled laborers earn anywhere from $10 to $25 per hour or more depending on the region of the country where they reside. The type of building being constructed also affects labor costs as larger structures may require more workers than smaller ones because there is more ground to cover during each phase of construction.
Contractors’ Fees
The contractor’s fee is another major factor affecting overall project costs. A contractor’s fee covers all aspects of project management including scheduling, bidding, managing subcontractors and ensuring that all work meets code requirements. Contractor’s fees vary widely depending on many factors including experience level, past performance record and overall reputation within the industry as well as geographic location within the country where they operate their business
Cost to build commercial warehouse
When new companies outgrow their current workspaces, they look to develop warehouses that expand and streamline their distribution and delivery processes. With rising e-commerce demands, industrial warehouses have become one of the most resilient assets in the real estate industry. Due to the wide range of products produced by companies, warehouses increase logistics efficiency in retail. The warehouses scale shipping processes and ensure product availability with minimal backorders.
Warehouses are large and complex projects, and we will discuss the costs of building a warehouse and how you can effectively maximize the available space.
TABLE OF CONTENTS
WAREHOUSE COST BY SIZE AND SQUARE FEET
The average costs for building a warehouse are $20 per square foot for the shell building. For small warehouses of 40 by 60 ft, the prices can be as low as $150000. However, for big warehouses of about 50000 square feet, the prices shoot up to $3,125,000. The price is affected by the size of the warehouse, type of materials, delivery costs, and construction methods.
Below is a rough estimate of costs on warehouses based on size and price. We sourced the following data from Strong Building Systems.
DIMENSIONS | SQUARE FEET | TURNKEY ESTIMATE |
---|---|---|
40×60 | 2,400 | $150,000 |
50×60 | 3,000 | $187,500 |
50×80 | 4,000 | $52,800 |
50×100 | 5,000 | $312,500 |
60×100 | 6,000 | $375,000 |
80×80 | 6,400 | $400,000 |
80×100 | 8,000 | $500,000 |
100×100 | 10,000 | $625,000 |
100×150 | 15,000 | $937,500 |
100×200 | 20,000 | $1,250,000 |
100×300 | 30,000 | $1,875,000 |
100×400 | 40,000 | $2,500,000 |
100×500 | 50,000 | $3,125,000 |
100×1,000 | 100,000 | $6,250,000 |
The shell building consisting of a concrete slab base costs about $20 per square foot, whereas the steel building framework from $7 to $12 depending on the gauge of steel used for construction. The costs in the table above are inclusive of land and grading. If one can obtain land and grading for significantly lower prices, it will decrease overall construction costs.
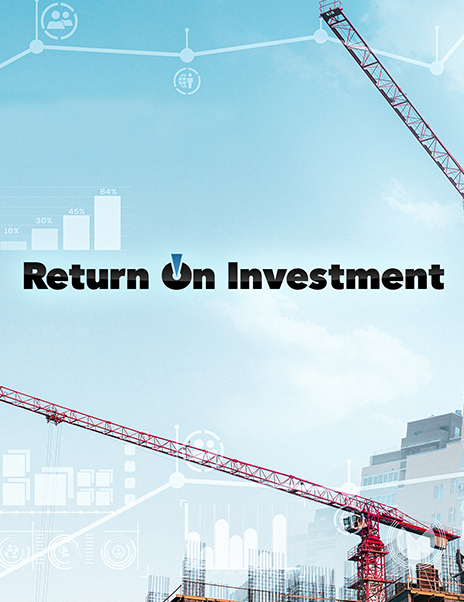
GET YOUR ESTIMATE
COSTS TO CONSIDER
Various costs encompass the construction costs of a warehouse. These are hard costs, soft costs, financing costs, and operational costs.
SOFT COSTS
Soft costs are among the hardest to estimate. Soft costs are not directly linked to the construction but are necessary for the operations of the project. Soft costs include permits, taxes, insurance, engineering and architectural design, and moveable equipment. If unplanned, soft costs can bring a project to a halt as they are unique in every project. Their uniqueness is part of the reason why they are difficult to estimate.
HARD COSTS
Hard costs are all the cumulative expenses directly linked to the physical construction. They are the foreseeable construction costs. Some of these costs are labor and materials. As much as these costs appear easily predictable, they fluctuate depending on the market conditions. Other hard costs include site development, grading, and landscaping.
FINANCING COSTS
One of the most critical construction costs is financing costs. Most clients finance their projects using loans. Owners, therefore, need to carefully assess anticipated costs and weigh whether they are receiving good value for money from their lender’s loan. There are three types of financing in warehouse construction. The first is the short-term construction loan, which an owner takes to cover project costs before obtaining long-term funding. The second funding type is bridge financing. A client secures this loan to pay off a standing construction loan. The final financing type is the permanent takeout financing that the client takes to finance the project in the long term.
LONG-TERM COSTS
These refer to the ongoing costs such as maintenance, utility bills, and upkeep. These costs dramatically fluctuate over the lifetime of a project. For instance, you can reduce your electricity bills by upgrading and insulating your warehouse. The upfront costs will be high, but in the long run, your monthly fees reduce. Other long-term expenses include property management, taxes, and insurance.
CONCRETE FOUNDATION COSTS
A concrete foundation supports all warehouses. They are not uniform concrete slabs like the ones an average house has. The concrete foundation is anchored with a rebar to support the structure from wind and seismic activity. Concrete slab foundations cost about $6 per square foot.
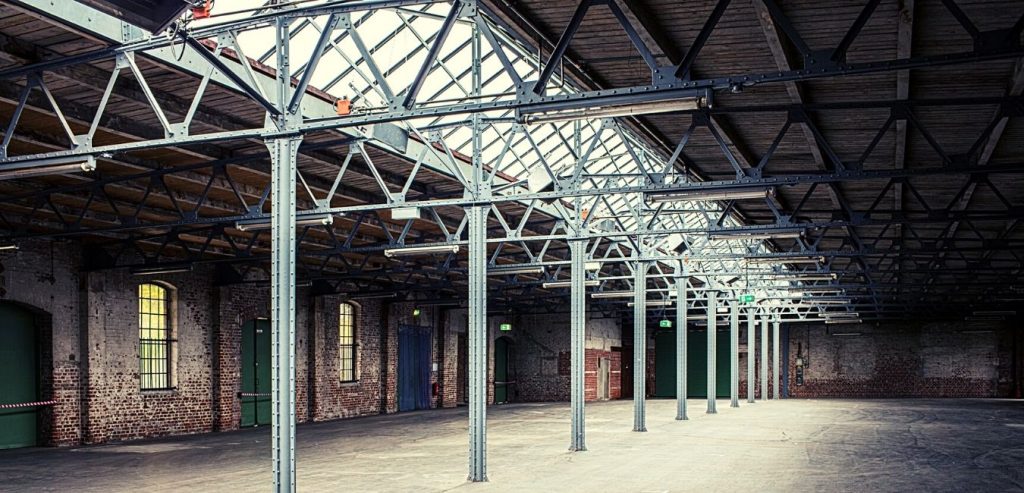
WHAT IMPACTS THE WAREHOUSE BUILDING COSTS?
The construction of a warehouse is a significant infrastructure investment. One needs to perform careful analysis on various factors that affect warehouse building costs. Some factors that impact warehouse building costs are the type of warehouse, location, and design. Below are some of these considerations.
INITIAL CONSIDERATIONS
There are initial considerations that have an immediate effect on costs. These are the volume of goods you intend to store in your warehouse, access points to market outlets, accessibility by staff members, and future scalability of the warehouse. The location of your warehouse affects its accessibility to the market, transportation costs of goods, and land acquisition costs.
SCOPE OF CONSTRUCTION
Your project’s scope also affects construction costs. The size of your construction project is one of the most significant factors that drive up construction costs. In an already constructed warehouse, the prospects of expanding scale up the construction costs. The scope of the project is coupled with the complexity of the project. The more the complexity increases, the higher the prices shoot up as the labor and material costs increase.
USE CASE OF THE BUILDING
The type of use brings in different designs for efficiency and gives better low-cost alternatives. A common consideration in warehouse design is cold storage. Some distributors and retailers need warehouses with cold storage if they are dealing with perishable goods. Incorporating cold storage leads to manipulations of the basic design as it will be necessary to add more rooms and facilities to accommodate the new designs.
DESIGN COSTS
The design team should design a warehouse in a way that fosters a good work environment. With different designs come different types of warehouses. Some warehouses to consider are the humidity-controlled warehouses and the refrigerated warehouses. Either of the warehouses mentioned above increases the material and labor costs as the architectural and engineering costs increase. The design needs to be precise to accommodate these functionalities.
ARCHITECTURAL DESIGN
The complexity of your architectural design increases with the type and volume of goods stored in a warehouse. If one has different kinds of goods with varying storage requirements, building a warehouse with multiple rooms might be necessary to accommodate various storage requirements. This will increase the construction costs as the design and labor costs will increase.
MATERIAL COSTS
The material costs vary with the type of warehouse and storage. The materials for a cold storage warehouse will cost anywhere between $150 to $170 per square foot, whereas the materials for constructing an average warehouse will be between $50-$65 per square foot.
The material costs also go up depending on the height and quality of construction you need. If you build a high warehouse, the material costs will substantially increase due to larger loads of lower floors.
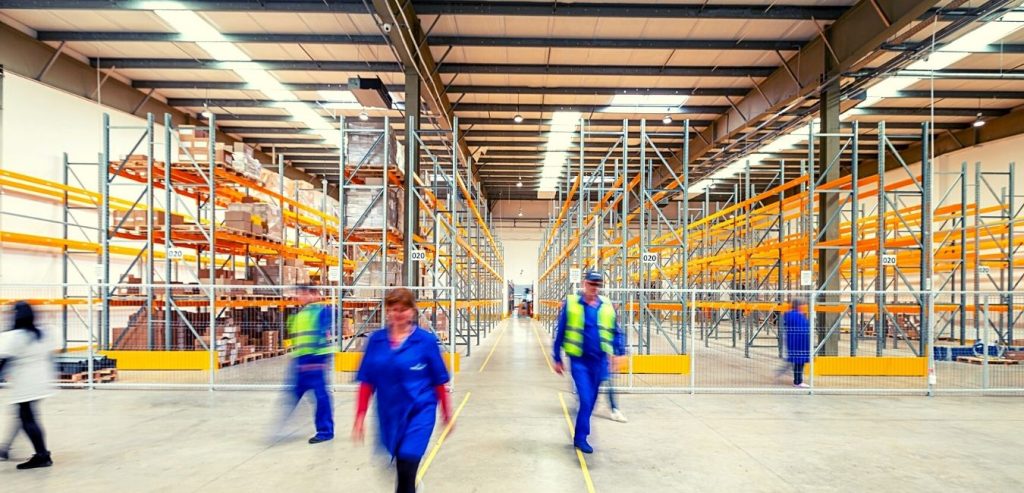
THE STAGES OF BUILDING A WAREHOUSE
Building an efficient warehouse is quite an endeavor. Before constructing a warehouse, you need to know the construction procedure to make your project a success. The construction of an efficient warehouse follows a four-stage process, as we will discuss below.
INITIATION
A good client should be knowledgeable and discerning on the type of project they need. This is also known as the inception stage. The project team makes the most critical decisions during the inception stage, and the client’s input is vital. Their decisions during the inception stage are not casual as they affect the effectiveness and overall project cost. During this stage, the team does careful feasibility studies to build the warehouse within the best budget.
If the client has not settled down on a location, this might be the perfect time for zoning and selecting suitable sites for constructing the proposed building.
In any construction, a wide range of stakeholders are consulted, and therefore, a project team should be formed as early as possible. The project team includes a structural engineer, architect, client representative, and contractor. The contractor is selected through a competitive bidding process.
PRECONSTRUCTION
The next stage in construction is the preconstruction stage. Preconstruction is the most critical building stage. After the appointment of consultants and the contractor, design starts during the preconstruction stage. The project team develops a professional design that meets the client’s needs and adheres to the relevant building codes. The design team conducts design in four stages. These are the preliminary design, schematic design, detailed design, and final construction design.
Proposals are prepared and cost during preliminary design, and an acceptable scheme is adopted.
After the preliminary design, the design team develops a schematic design in more detail, enabling the client to approve spatial arrangements, materials, and appearance. They should not change the building layout and construction method during this stage.
The following design is the detailed design where all the construction details are reviewed and the cost estimate refined.
After the preliminary design, the cost consultant prepares the project’s cost estimate. As the design evolves, this estimate is updated. The general contractor can renegotiate the contract terms during the preconstruction stage.
During the preconstruction stage, the project team also embarks on a more detailed feasibility study as they already have the cost estimates for construction. The feasibility studies should establish the following factors:
The type of warehouse and available alternatives
- Cost savings on either prefabrication or new construction.
- Potential incentives: There are many potential incentives often overlooked during construction. These include project financing, employee training, tax reductions, land donations, and operation cost reductions.
- Recruitment of staff and training implications: This should be done to determine the wages and budget necessary for training programs.
- Regulatory requirements: Before starting construction, it is necessary to assess the potential sites, review federal, regional, and local requirements and the zoning restrictions as these can affect the viability of a project. In some instances, areas with heavy traffic, air, or noise pollution may prompt an environmental impact assessment to determine their implications on a project.
- Cost outline with an assessment of both operational and maintenance costs.
- Work plan for project completion.
PROCUREMENT
After setting out the roadmap in the preconstruction stage, the next step is procurement. Here the project team obtains the equipment and necessary materials for construction. The complexity depends on the size of the project, availability of resources, and the expected project commencement date. Many construction companies are equipped with in-house construction teams that make procurement easy. It is also a chance for cost savings by the contractor as it increases the profit margins.
CONSTRUCTION STAGE
The construction stage is what most people relate to due to its visibility. The construction stage is when the actual groundbreaking occurs. However, the bulk of the work is accomplished during the preconstruction stage.
The planning pays off during this stage. The project team holds a preconstruction meeting. This meeting is to ensure everyone in the project is on the same page. It irons out issues such as accessing the job site, quality control, storage of materials, and working hours. The working hours are always dependent on the role played by the worker. If poor planning rolls out during the construction stage, it can lead to severe cost overruns and delays. Once the meeting is over, work can commence. Usually, contractors avoid pitfalls during the construction stage by employing software solutions.
The second order of business is earthwork and foundations. Soil is added or removed from an area to create a level area for trucks transporting material to the site. Concrete is then poured into the area excavated for the foundation.
The next step is building a framework on top of the foundation. This framework typically consists of heavy metal girders and beams. A lighter skeleton is then made over the heavy framework to contain the windows and doors. Metal sheets are then added to the framework for roofing. A layer of insulation is then added and systems such as heating and air units. All other units, such as offices, are then made operational. Pathways are marked, and specialty features added. With this, the warehouse is ready to move to post-construction.
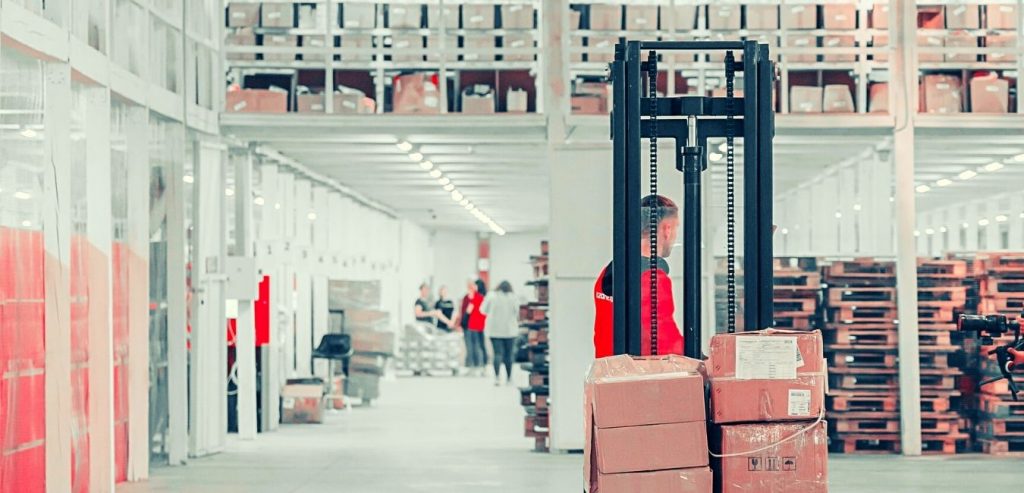
POST-CONSTRUCTION
During the post-construction stage, all the work is complete, and the project is ready for handover. However, there are a few processes that need completion before the final handover of the warehouse. The post-construction process is subdivided into three stages. These are:
- Warehouse commissioning
- Owner occupancy
- Project closeout
WAREHOUSE COMMISSIONING
Here, the project manager headed by the project manager conducts an inspection to ensure everything was accurately done. These inspections are easy to pass since many inspections correct the defects that crop up throughout a project’s lifetime. During this inspection, the project manager prepares a snag list. This list notes some problems such as forgotten project aspects, material and design issues, and poor craftsmanship.
After checking everything, the project team trains the client on proper usage and maintenance of the warehouse. This considerably improves the lifetime of the warehouse.
OWNER OCCUPANCY
After the training is complete, the owner then takes occupancy of the building. The warehouse warranty is active during this stage, and the owner has enough time to assess the systems and equipment installed.
PROJECT CLOSEOUT
Project closeout is the last stage of construction. The project team reviews the contract and ensures any legal burdens are taken care of. This would be a good time for the builders to perform a post-project review and identify things they need to improve on in upcoming projects.
The timescale of building a Warehouse
The time needed to build a warehouse is dependent on several factors. However, it is common knowledge that this time has significantly reduced over the past ten years. According to World Bank data, the time necessary to build a warehouse ranges from 86 days in the United Kingdom to 213 days in France. It takes an average of 165 days to make a warehouse in the United States. As building time declines, building costs increase due to the increased complexity in a building.
The building time factors are the type of warehouse, location of the site, energy-related costs, and materials.
CONCLUSION
By now, you are ready to get your warehouse project rolling. Many factors influence the costs of warehouses, but the common factor is the ever-increasing demand for industrial space. Other factors affecting cost include the location and size of your warehouse.
There are many dimensions and design types that you can consider depending on your intended use and budget. The inventory methods you apply will also depend on the kind of warehouse you settle for. The type of warehouse you choose also influences the future service costs. Always consult a cost expert before starting your project to get the best possible quotations.
Finally, it would help if you considered time lag considerations when constructing your warehouse. These factors affect plans in your organization and keep adding to the workforce and costs. The implications can also affect the quality of service delivery and affect the supply chain.